Dec. 11, 2023
A View from the Plant at Mid America Paper Recycling
Alan Surdyk, Plant Manager at Mid America Paper Recycling, and his team work to keep the recycling facility as efficient and effective as possible. Working as a sales representative for Mid America Paper Recycling in 2003, Surdyk became Plant Manager in 2004. A member of the Mid America family that has owned the independent brokerage, processor, and exporter of recovered paper for four generations, Surdyk manages the plant team and is on the front lines with it every day. He’s charged with running several operations, ensuring that high-speed sorting, baling, cutting, and compacting systems are operational, as well as organizing load logistics and coordinating shipping and receiving among other things.
“Alan has done a nice job of working with our teams running waste materials through the plant in an efficient manner,” says Don Gaines, Chief Operating Officer of the company. But how does the team handle all of these used materials, including several grades of paperboard, corrugated, SOP, SUS, DLK and more?
The secret sounds cliché, Surdyk says, but it’s true. “It’s the people on our team. I have been operating the plant for over 20 years, and many plant personnel have been working for Mid America Paper Recycling much longer than that. With so many companies now wanting an ‘all-in-one’
recycler that not only accepts various grades of paper, but also metal, plastic, and glass, it takes the valuable experience and knowledge our team has to know how best to process everything we handle.”
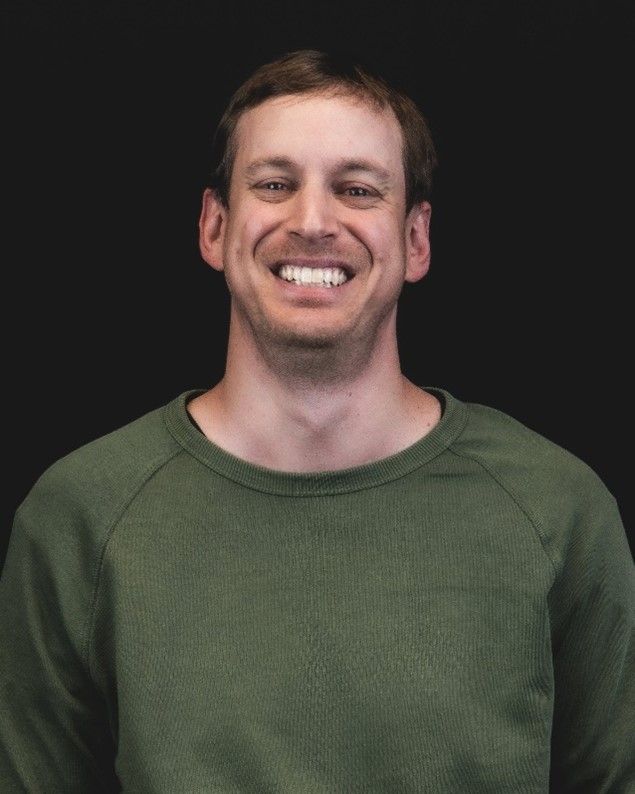
Alan Surdyk, Plant Manager.
Gaines echoes the assessment. “Our experienced team helps deliver quality fiber to consuming pulp and paper mills and provides detailed information that we use to help educate our suppliers.” The goal? “We want to Grow the Worth of Their Waste,” he explains.
A typical day in the plant starts at 6 a.m. when Mid America Paper Recycling’s fleet of trucks hits the road. The team picks up material from local customers using more than 125 truck trailers. “We also receive loads from all over the country,” Surdyk points out. “Our plant team then unloads the trailers and separates the materials into 51 different grades before weighing them.
“We then process the various recyclables and ready them for outbound shipping, often by baling, or compacting loads of the material,” Surdyk explains. “Once enough paper is baled to make a full load (the equivalent of 42,000 to 56,000 lbs., depending on the grade and type of material), we then ship the load to paper mills all over the country – and sometimes around the world.”
So many grades of paper look and feel alike that the plant team must communicate with each other, stay transparent with suppliers to educate them on proper sorting methods, and strive to achieve the highest possible return on recyclable waste. “That’s why educating our customers is very critical,” Surdyk notes. “When we help our customers achieve recycling success, it is a win-win for them and Mid America Paper Recycling. It makes me happy to be a part of a team that is always looking for bigger and better ways to operate. If you’re not changing and upgrading, you are being passed up by the competition. The changes also include evolutions in our paper sources. We are always looking to create new partnerships with suppliers and buyers.”
While it’s a dirty, gritty livelihood, Surdyk finds plenty of ways to keep the crew motivated. “It’s a challenge many companies face,” he admits, “and we are no different. We treat the crew to lunch when they do a good job. Sometimes I’ll provide different clothing or gift certificates to show my appreciation. At the end of the day, it comes down to how everyone is treated. The crew wants to know that someone has their back. They also want us to know when they have done something well. Communicating positive messages, and providing small incentives is often my approach.”
Zero-waste initiatives
Presenting a clear pathway for fiber recycling includes Mid America Paper Recycling’s zero-waste and service goals. “Both service and zero waste in our industry are not considered ‘extra,’” Surdyk says. “If we are not providing top-tier service, someone else will. If we are not doing everything in our power to recycle items instead of landfilling them, someone else will. We regularly wow our customers by providing a service that doesn’t just meet their expectations, it surpasses their expectations.”
Too often, people get comfortable with the status quo, he admonishes. “If you do ‘what you have always done,’ it can lead to a lack of growth. We are always upgrading. We recently added some new machinery to the plant, such as our new American Baler baling system, and a few new forklifts. This equipment is streamlining things and helping us to be more efficient. We are always looking at new ways to position our plant team as well. We evaluate labor-intensive processes, and whether we need two people or one to perform certain tasks. We have always re-evaluated the plant processes to utilize labor in the best way possible. Another example might be whether we need to begin transport on trucks at 6 a.m., or should we start them in the middle of the night to avoid traffic and reduce freight costs? There are many other examples. We must constantly try new things and innovate. Otherwise, someone else may pass us by.”
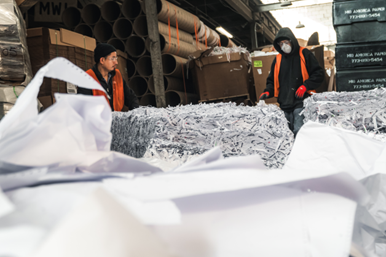
Teamwork and good communication are vital to the plant's operation
Surdyk acknowledges the recycling company and its customers and supplier-partners face challenges daily. “The materials we recycle are commodities. That means pricing can change and change often. It’s difficult to explain to a supplier that an item they were paid for over the last year is now something we must charge for. Also, packaging is not always recycle-friendly, so we must adapt and handle certain items in the best way possible. It all goes back to our zero-waste goals of making great efforts to find the right home for tough-to-move items. This is why educating suppliers is crucial. Making them aware of the challenges we face helps them understand how we can help them turn a non-desirable item into something that has value and can generate revenue.”
As the year winds down, the plant crew expects to complete installation projects, such as adding new warehouse heaters and updating some of the recycling equipment. “We are also always training new employees to support others in different positions,” Surdyk summarizes. “Currently, we are training an employee to unload trailers. And the team is always coming up with new ideas for improvement.”
Reviewing his 20-plus years of experience in the plant, Surdyk recalls many innovations. “The plant operations are always changing. When I first started here, things were quite different. There were many manual functions. We have automated quite a bit, and I’m proud of the improvements we have made. They start with three things: experience, communication, and flexibility.”
To assess and upgrade your recycling operation, take our quick, free Waste Audit Survey. Visit https://www.midamericapaper.com/waste-reduction-audit.


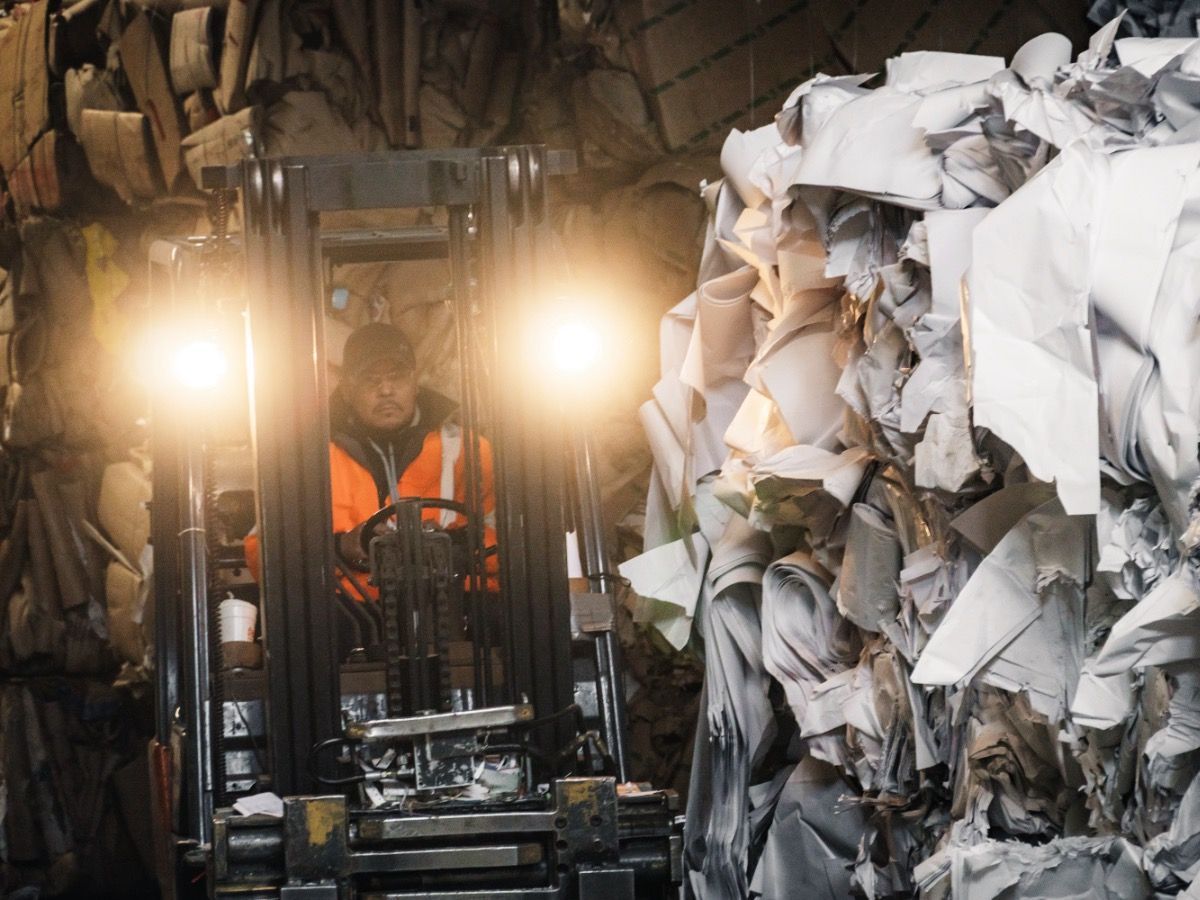
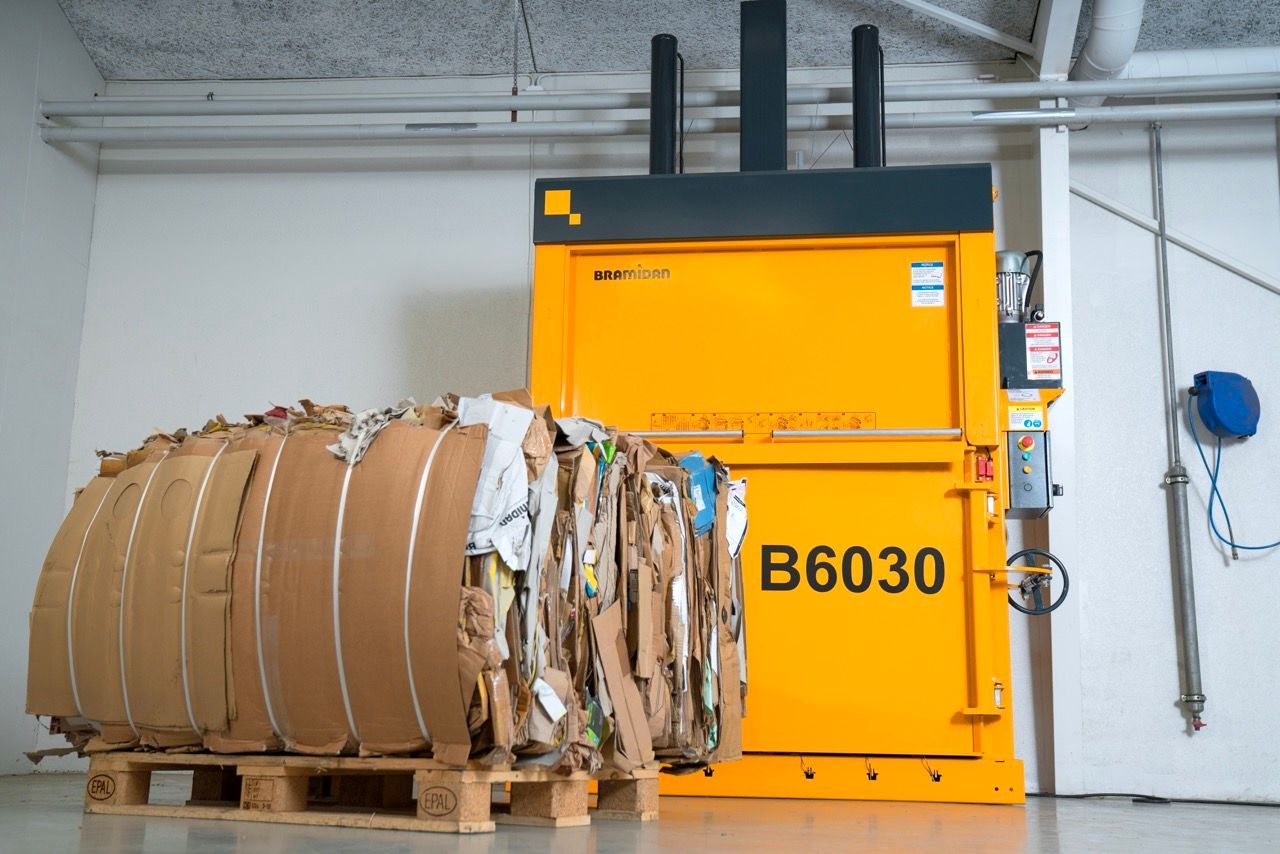