Did You Know All the Dangers of Dust?
Especially if it’s in the form of dust present in the facility where they work. Due to a growing number of catastrophic fires and explosions caused by combustible dust in the last decade, the Occupational Safety and Health Administration (OSHA) as recognized combustible dust as a hazard.
Did you know that facilities had a Sept. 7, 2020 deadline to comply with the updated Standard 652, a requirement set by the NFPA?
There is evidence that many factories and production facilities handling combustible dusts are unaware of the hazards. Therefore, the NFPA decided to introduce the standard to promote further awareness and protect worker safety. Basically NFPA 652 requires pulp and paper mills, manufacturing companies and other businesses that generate dust to perform a Dust Hazard Analysis (DHA) based on the updated steps to prevent and manage fire and explosion hazards related to combustible dusts.
Issued by the standard, the new DHA terminology differentiates this analysis from more complex forms of process hazard analysis methods currently found in industry. If you have processes that create dust or use powders, then you have a responsibility to determine if you have a combustible dust hazard. Why? For one, combustible dust-related fires and explosions are a national problem. In 2016, the U.S. reported 31 explosion incidents that caused a reported total of 22 injuries and three fatalities.
Updated in 2019, the NFPA 652 requires facilities to demonstrate progress in completing a DHA in the years leading up to the deadline and the facilities must continue to review and update their DHA every five years. The NFPA 652 standard applies to all facilities that deal with combustible dust. NFPA 652 defines combustible dust as “a finely divided combustible particulate solid that presents a flash fire hazard or explosion hazard when suspended in air or the process-specific oxidizing medium over a range of concentrations.”
Clearing the air
So what’s involved in a DHA? The process identifies threats and creates a plan to manage fire/explosive threats from dust. Systematically reviewing the safety of both new and existing facilities, a DHA can get manufacturers on their way to preventing a flash fire or explosion hazard associated with the presence of combustible dusts and combustible particulate solids. NFPA 652 is the starting point for this analysis, and acts as a step-by-step guide, identifying hazards and what to do next.
OSHA, together with local authorities, enforce the NFPA standards. Identifying and evaluating these potential fire hazards as required by the NFPA is also required by the Environmental Protection Agency (EPA). OSHA assumes a facility’s dust is combustible unless the company has the test results to prove the dust is calculated to have an explosive value of zero.
The analysis examines all areas of a facility where combustible dust is present and identifies hazards as related to explosions and fires. A DHA categorizes each area of the facility as “Not a Hazard,” “Might Be a Hazard,” or “Deflagration Hazard.” Additionally, the DHA helps identify where a facility is not compliant or has areas of concern, and also offers solutions and recommendations.
Chapter 7 of NFPA 652 provides detailed descriptions and explanations of DHAs. You can also find a complete, step-by-step example of how to create a DHA in Annex B. The Center for Chemical Process Safety publishes Guidelines for Hazard Evaluation Procedures, covering simple and complex systems and techniques with examples.
“There can be high levels of dust in pulp, paper and packaging plants, so safety is a priority,” mentions Mid America Paper Recycling President Paul Pirkle.
“Combustible dust must be properly contained and collected. Ignoring dust hazards can result in serious consequences, so we want our suppliers and customers to be safe and aware of the updated standard and the new September deadline.”
Dealing with dust
Where to start? To determine if your facilities are applicable to the NFPA 652 standard, having an initial screening using a dust cloud dispersed around a strong ignition source will determine whether any dust in the facility will ignite. Many commercial test labs offer a low-cost test to establish whether a dust sample is combustible.
If combustible dust is present and hazard areas are found, a DHA will be needed. Specific material tests and procedures depend on the industry and business involved.
According to the NFPA, the NFPA 652 standard pertains to all industries having processes that can generate combustible dust, but specifically addresses the metal, agricultural, chemical and wood processing industries. OSHA also reports the risk of combustible dust explosions is present in industries processing food, grain, tobacco, paper, rubber, dyes, plastics, pesticides, metals, pharmaceuticals and pulp.
The process
Basically, if combustible dust exists, professional engineering consultants are available to assist facilities with this evaluation by fully evaluating any combustible dust threat to the facility based on compliance with all applicable national codes and standards. Everyone involved in a DHA should be familiar with all the governing NFPA standards. Your local authorities and fire marshals with jurisdiction can also provide further safety details.
- The DHA is required to be performed in accordance with NFPA 652, chapter 7. Observations should be documented (the updated edition of NFPA 652 relates to managing the dust-related fire, flash fire, and explosion hazards in industries that use dust collection and handling equipment, or that have processes that may generate combustible dust).
- Results of the DHA require a plan of action to be implemented.
- Maintaining the DHA and reviewing and updating the process is required every five years. Once the DHA is complete and the facility is certified, the best way to reduce worker exposure to toxic dust is to install a multifilter dust collection system.
Capturing dust at its source prevents it from expanding throughout the plant. Accomplishing this requires efficacious, NFPA-acceptable equipment or devices, Pirkle adds.
In some cases, any existing dust collection systems will need to be inspected and upgraded to ensure compliance with these guidelines. “Some systems and dust collectors currently in use may not be acceptable. The right equipment that properly isolates and collects toxic dust according to the NFPA 652 standard are available, and using them not only helps prevent hazards, it can even reduce facility costs.
Also, it can reduce indirect labor costs and time associated with emptying dust into large open-topped containers, which can be messy and dangerous. Further, the containers can take up a lot of space in a facility. Freeing up this space benefits the facility.
When selecting dust control equipment, look for an experienced supplier in your industry that complies with current OSHA, NFPA and EPA requirements. Compliant dust collection and mitigation equipment like those distributed by Kernic Systems (www.kernicsystems. com), Burlington, ON, are available in a variety of configurations. Kernic also provides air pollution control equipment to meet any challenge with safety and efficiency in mind, as well as numerous services and accessories to allow users to breathe easier.
For more information on DHAs and the NFPA standard, contact the NFPA at www.nfpa.org.
Contact Mid America Paper Recycling (midamericapaper.com) and Kernic Systems (kernicsystems.com) to get started on a Dust Hazard Analysis.
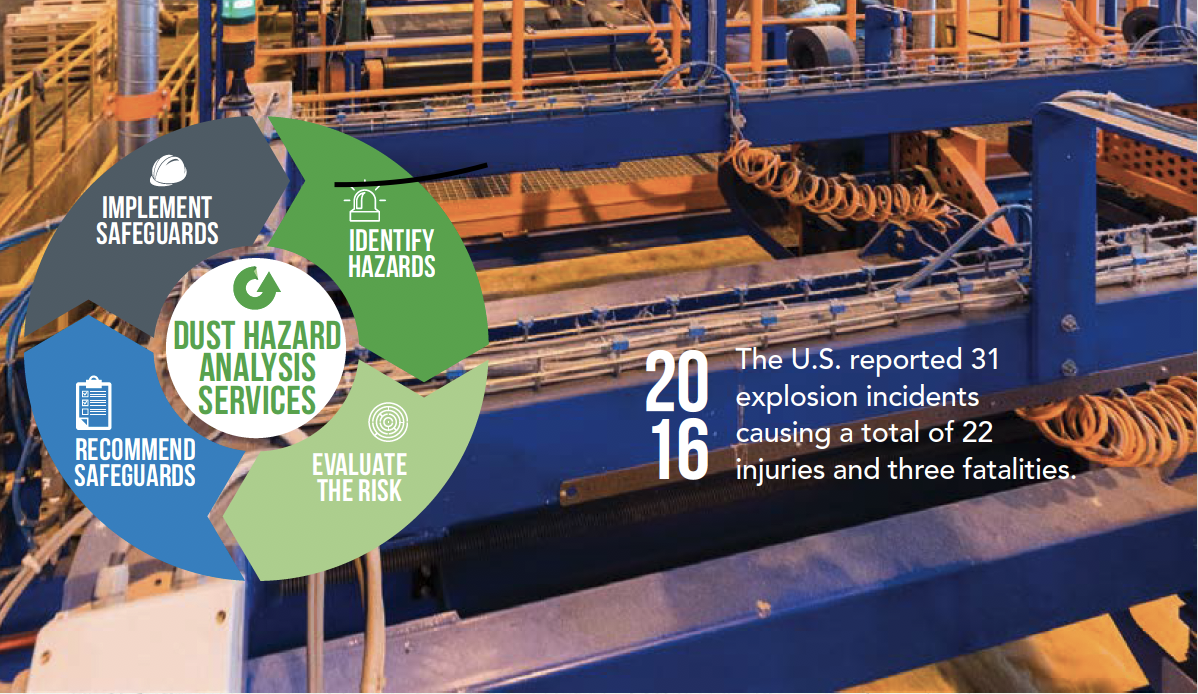
Leave a Reply
Your email address will not be published. Required fields are marked *

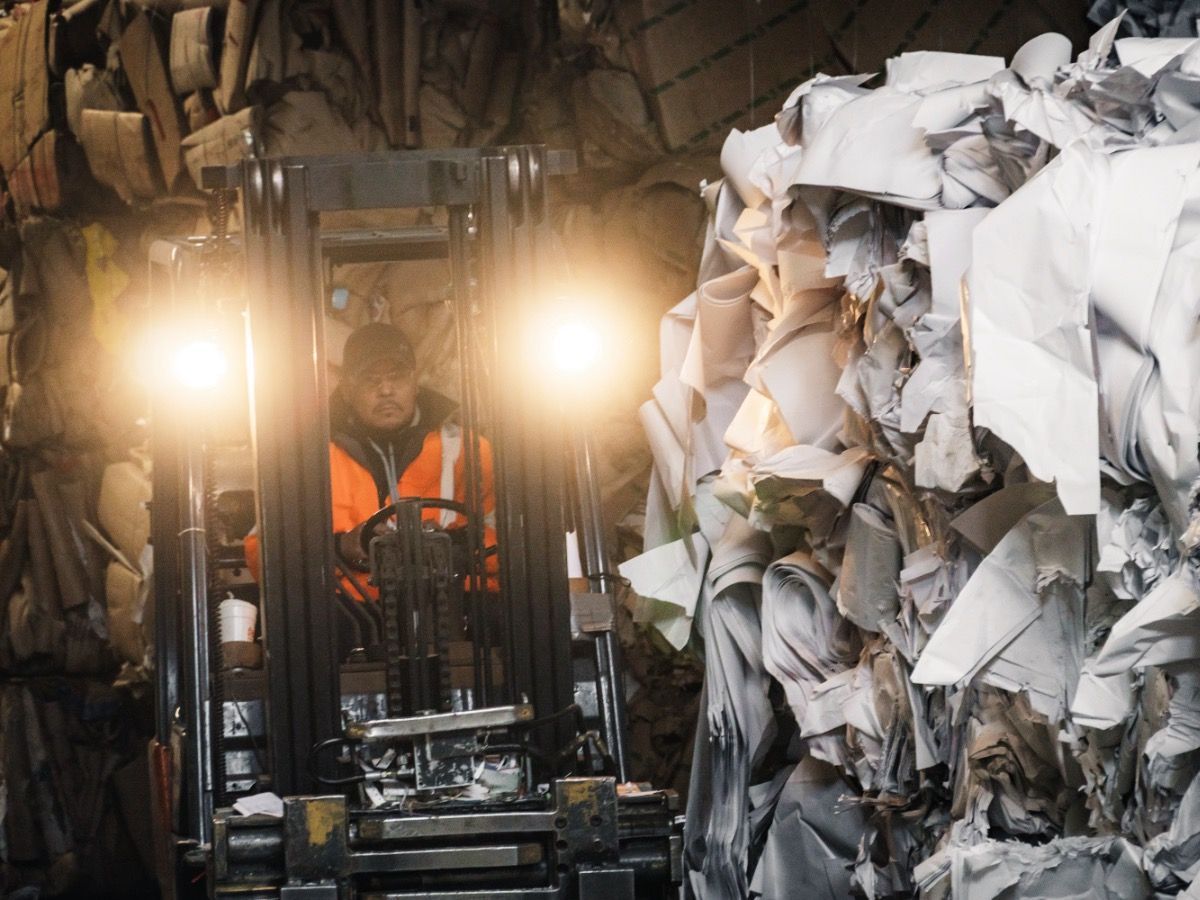
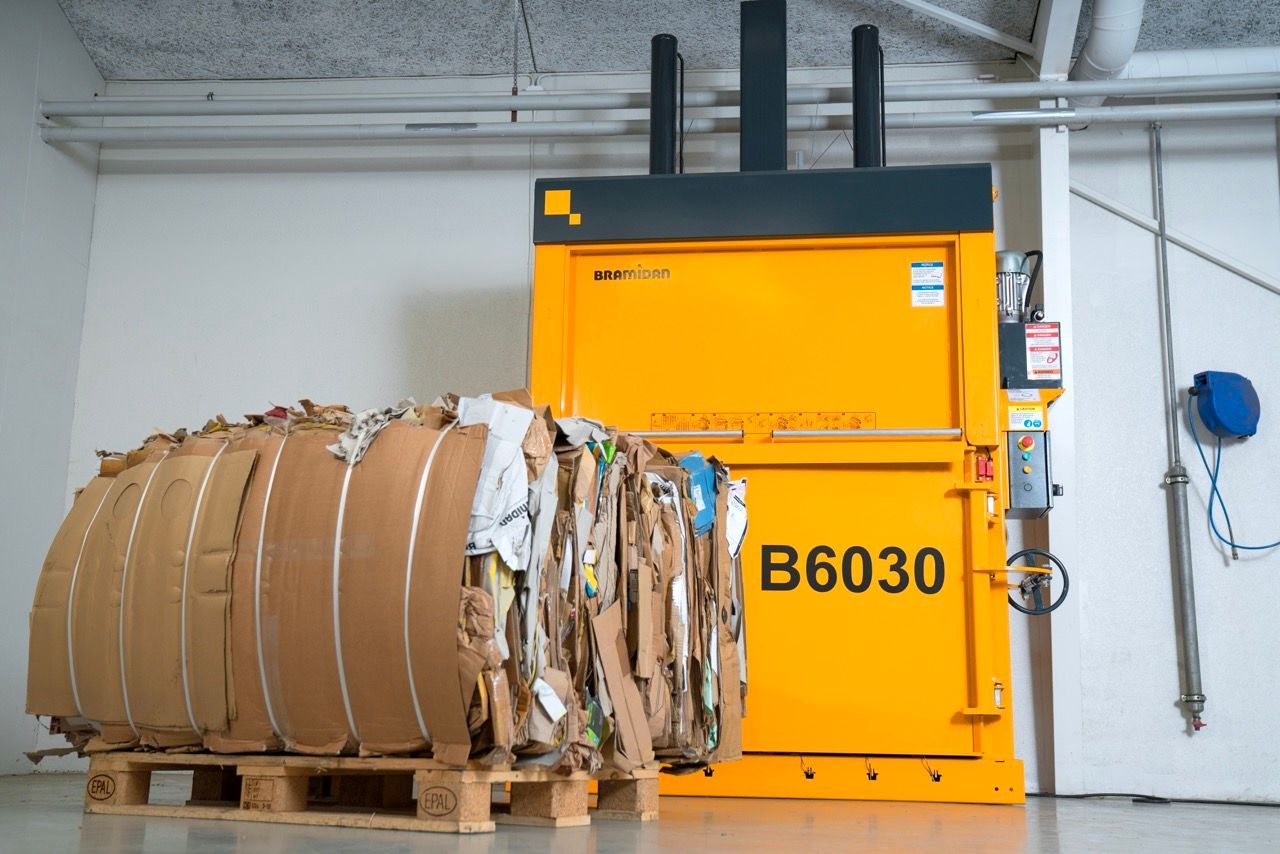