Strengthening the Supply Chain During the COVID-19 Crisis
The rapid spread of COVID-19 has introduced new challenges across the business landscape. The worldwide disruption of business as usual due to the Coronavirus has substantially affected supply chains and the manufacturing industry’s ability to deliver product and drive revenue in the recycling and paper mills industries. But responding with a practical and an informed, proactive approach to scheduling, planning, and tracking loads throughout the chain can help navigate uncertainty and gain clarity in these changing times.
Resilience and readiness mean working with partners to provide business support and continuity. Strengthening your supply chain management or (SCM) — the wide range of functions required to plan, schedule, control and execute the flow of That’s because it means tackling big issues such as compliance, supplier relationship management, risk and disruption, responsible sourcing, and transparency.
But as the novel coronavirus outbreak has rapidly expanded over multiple geographic regions, undoubtedly main concerns are being raised about how it will affect the supply chain. In just a few months of the pandemic, disruptions became prevalent. According to the Centers for Disease Control, establishing a disruption preparedness strategy and ensuring that employees are safe is a must, as is regularly updating personnel on CDC recommendations. Employees should also be equipped with as much personal protective equipment (PPE) as possible and strive to maintain safe production facilities.
Recycled materials must leave the mills as safely and economically as possible — there are several integrated processes and steps to optimize incoming and outgoing material, information and capital. Supply chain optimization is one initiative that appears on the to-do lists of many businesses but is frequently sidelined. That’s because it means tackling big issues such as compliance, supplier relationship management, risk and disruption, responsible sourcing, and transparency. But as the novel coronavirus outbreak has rapidly expanded over multiple geographic regions, undoubtedly main concerns are being raised about how it will affect the supply chain. In just a few months of the pandemic, disruptions became prevalent.
According to the Centers for Disease Control, establishing a disruption preparedness strategy and ensuring that employees are safe is a must, as is regularly updating personnel on CDC recommendations. Employees should also be equipped with as much personal protective equipment (PPE) as possible and strive to maintain safe production facilities. Next, rethink existing strategies, determine vulnerabilities and address as many as possible to guard against supply and demand shocks as material supplies may continue to slow.
Transparency pays
Transparency plays an essential part in an effective recycling supply chain. Mills and their customers are beginning to expect transparency along with a firm stance on ethical practices. Maintaining clear, upfront views and visibility are proactive measures. According to data analysis firm Thomas Insights, maintaining supply chain visibility is a proactive and sustainable measure most businesses can practice in disruptive times. Knowing what the status of production and loads are during supply chain activity and being able to readily respond on this status while still meeting demand can strengthen your resilience when working to mitigate risks from disruption.
“We must continue to work diligently to make sure we are communicating and proactively communicating with one another and finding solutions,” says Mid America Paper Recycling President Paul Pirkle. “What we do daily impacts the lives of many other people; we can achieve so much when we apply a positive attitude.”
Triumph with technology
Having a contingency plan in place means using technology to cope with and better manage production flow and supply chain issues to achieve as much continuity as possible. With the abrupt changes we’re all experiencing, supply allocation decisions can be made easier through thoughtful leadership and innovative leveraging of technology, Thomas Insights reports. Transportation management technology systems build more robust logistics within the supply chain that may help meet new challenges in demand planning, sourcing, production, inventory management, logistics, storage, and shipping. Using continuous improvement processes and reverse logistics technology can improve the tracking of pre consumer recyclable loads, finding the right high-grade recovered materials and timely pickup and delivery. Manufacturers can provide and gain access to data by joining supply chain information-sharing networks and investing in supply chain data management services.
Technology can also expedite accessing, capturing, analyzing, integrating, interpreting, and executing supply chain data in myriad ways. Knowing the status of production at the mills and/or at the supplier level and being able to readily respond to supply-side questions, concerns and issues while meeting demands strengthens supply chain resilience. An improved transportation network can help keep operating costs and the costs of purchasing, production, and throughput stable.
Risk management
Risk management forecasts and evaluates financial risks and identifies procedures to avoid or minimize. A supplier bottleneck, a cybersecurity breach, or disruption that the country is currently experiencing with COVID-19 affect the entire supply, with consequences that reverberate up and down the chain and ultimately impact an organization’s profitability and reputation. Over-concentrating supplier dependency in one area is a risk that can expand profoundly during times of economic uncertainty, Thomas Insights reports. Moving product or production across alternative sources better avoids the risks of over-reliance in one geographic location and instead apportions supplies through a diverse supplier base across different regions, the research firm adds. Supply managers can also mitigate risks by:
• Conducting an audit with documented response procedures
• Improving supply chain visibility
• Maintaining standards with an effective compliance program for suppliers – establish a continuous improvement program
• Staying informed and educated about relevant compliance programs
• Developing meaningful relationships and partnerships with critical suppliers using a structured Supplier Relationship Management (SRM) program to improve transparency
• Managing the risk of raw material price volatility with financial hedges, operational hedges, and price increase controls
• Improving supplier scorecards to ensure they are appropriate for individual suppliers rather than using a one-size-fits-all approach
Timing is critical
The recycling supply chain is complex and circuitous. Because of this, effective supply chain management requires change management and partner collaborations to effectively align with and communicate with all participants. That’s nowhere near as easy as it sounds, but relationship building is important. Providing additional efficiencies, benefits, higher profits, and lower costs takes two-way communication between recycling brokers, suppliers, and customers. Ask any paper mill.
“We want to grow [our base of] strategic partners we can call and work with,” says a recovered fiber operations manager from one paper mill/recovered paper recycling company. “When we ask them to deliver another 1,000 tons or need to sell off 1,000 tons and they say, ‘it’s no problem,’ that’s someone we want to do more business with.” Timing is crucial. “We try to match up our supplies when they come in when mill customers need them,” Pirkle notes. “That’s very tricky. Our teams are like air traffic controllers, matching supply and demand all day, getting the timing of incoming and outgoing tons right.”
Working smart
As the business landscape shifts in these uncertain times, recycling businesses and the mills that engage them are working smarter to recover valuable paper/fiber feedstocks. While manufacturers have long been reusing and repurposing scrap materials in various ways, finding untapped fiber sources and increasing “easy access” to clearly marked material drop-off bins and receptacles at the manufacturer, distributor and retailer level are worth the effort. Building managers can be your company’s eyes, ears, and voice. Build relationships with them that will help increase recycling and provide handouts to building managers who support recovery efforts (trash collection adds costs, but recycling doesn’t). These brochures can inform them about how the scraps, rejects, trimmings, and other “stuff” that ends up on the factory floor can be transformed into something valuable.
Keep such handouts as visual as possible — use colorful graphics wherever reasonable to convey recycling messages and exact drop-off locations in the building. And remember to follow city requirements, as necessary. There are countless reasons to strengthen the supply chain. Managing risk plays a major role, especially now. Even if your business has managed to avoid significant supply chain disruptions so far, 2020 will be remembered as a year of total disruption in the world. It pays to be prepared and organized.
Leave a Reply

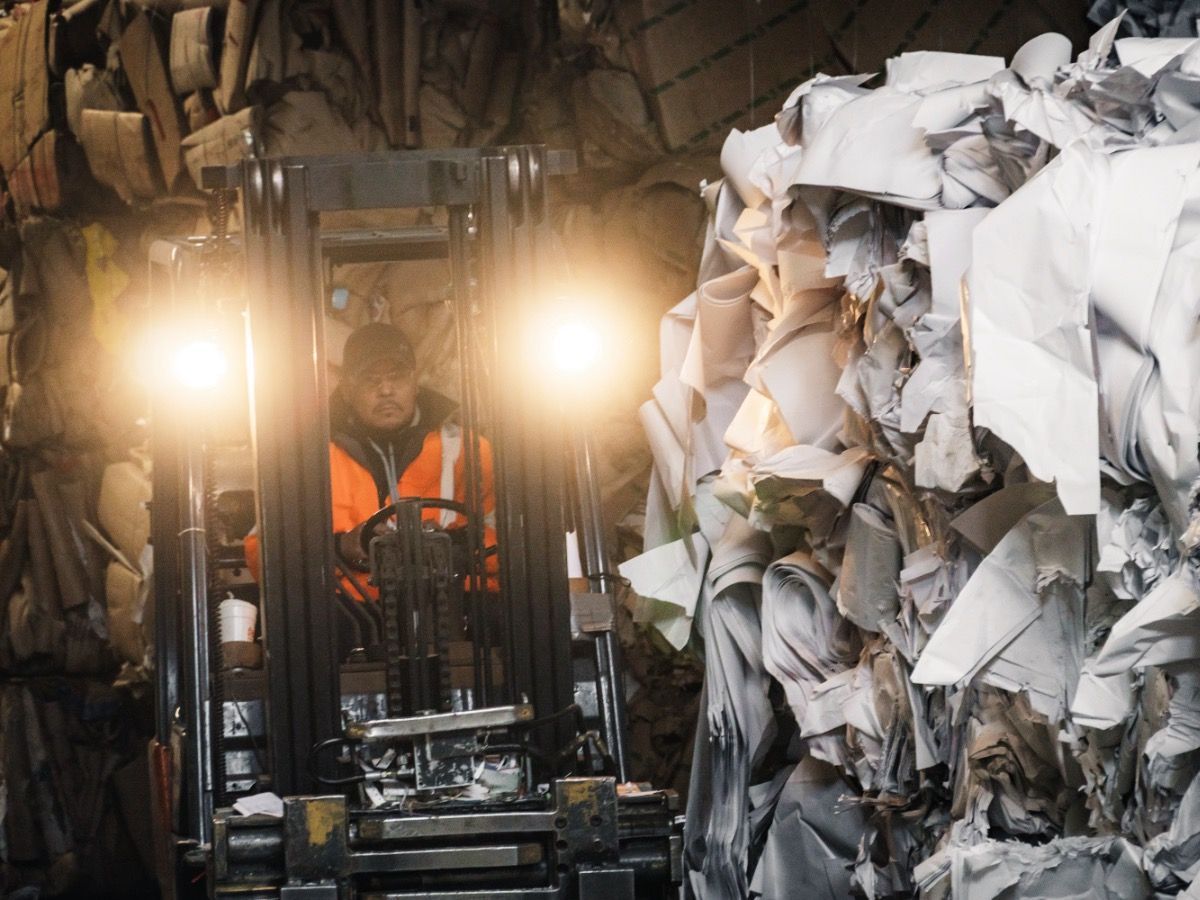
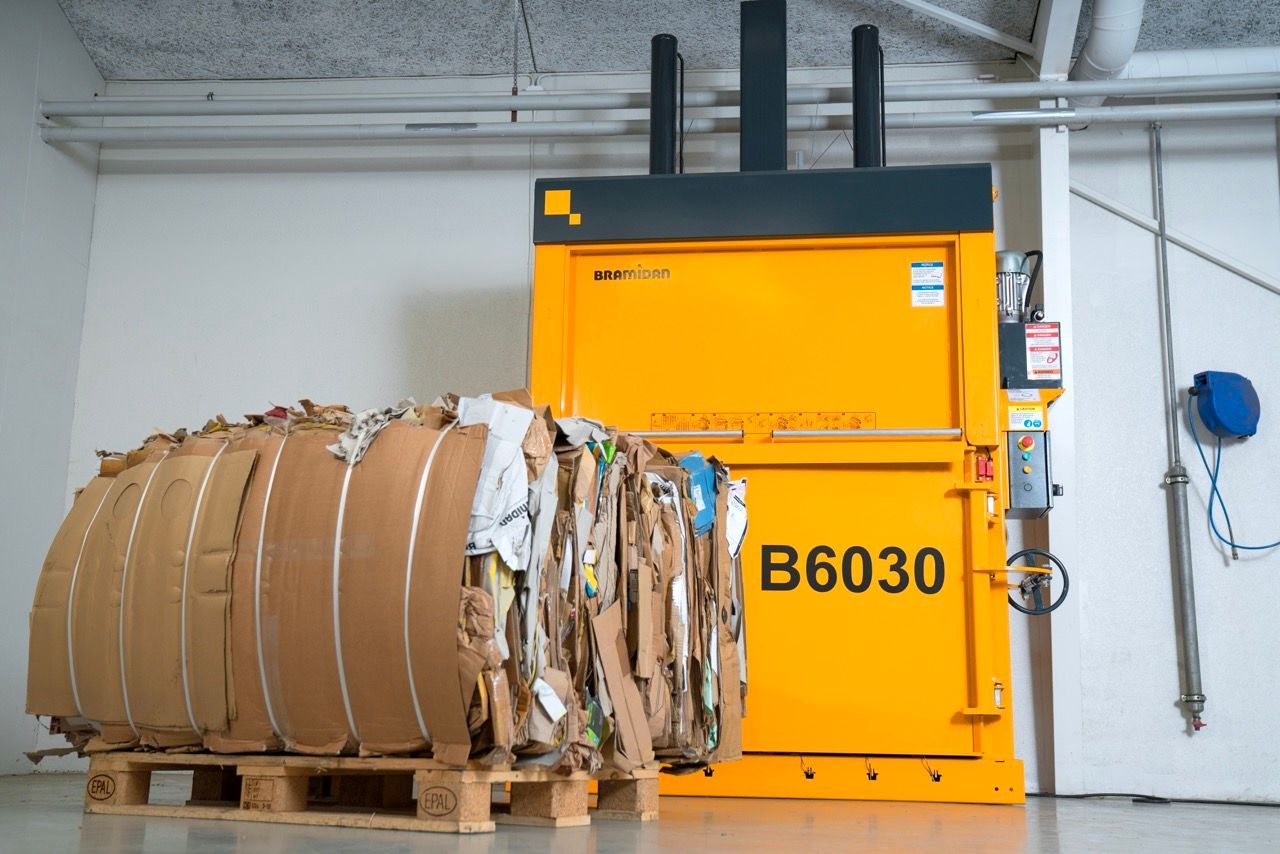