Safety Tips
“At the end of the day, the goals are simple:
Safety and security.” — Jodi Rell, former Governor of Connecticut
Obviously, some work environments are more dangerous than others, and “safety first” is more than just a saying. We’d think by now, everyone would’ve learned those two critical words. But did you know in the manufacturing sector, there were 22,040 injuries, and 49 deaths in 2016, and in transportation and warehousing, there were 23,490 injuries, and 46 deaths (according to the National Safety Council)?
Pulp and paper workers are exposed to many hazards and suffer numerous injuries each year. Injuries such as lacerations, being crushed by huge weights, being burned, or getting severely cut by a saw.
The Bureau of Labor Statistics reported 10 fatalities and 2,840 injuries/illnesses in the paper manufacturing industry in 2018. To ensure everyone’s safety, employers must be keenly aware of the primary safety guidelines for employees working in the pulp and paper industry, and plan if the team is working from a ladder, catwalk, or roof.
Regulations like OSHA 29 CFR 1910, ASTM F739-12 for Permeation of Liquids and Gases and NFPA 2112-Standard on FR Garments, equipment improvements and the proper use of Personal Protective Equipment have resulted in the decline of critical statistics over the years. But even one injury is too many, as the premiere safety experts say. When enhancing safety in the pulp and paper industry, it’s important to plan ahead, assess the risk and use the right equipment.
Safety equipment
All workers should wear the required personal protective safety gear (PPE) while on the premises. Equipment must be kept clean and maintained, especially now with COVID-19. Wearing loose clothing or jewelry when on the job should be avoided. People with long hair must keep it tied back when working with moving machinery.
Risk assessment
To protect yourself and those around you, always be aware of what could go wrong and what you can do to prevent a potentially dangerous situation. Never take unnecessary risks and stay calm if you find yourself in a perilous predicament. Every company should conduct a risk assessment to identify and prevent work hazards.
Safety training
Safety training is essential when working in a plant. Employees must be aware of all safety procedures, especially as they pertain to their specific position. Special training should occur periodically to reduce the risks of accidents.
Emergency evacuation drills
Fire and other evacuation drills are an excellent way to help everyone understand the proper conduct in the event of an emergency. Employees should be familiar with all emergency exits and fire extinguisher locations and how to use a fire extinguisher. It’s also important to determine which machines should be shut down and which can be left running if a real emergency building evacuation occurs.
Working with tools
All tools should be kept clean and in perfect working condition. Any defects should be immediately reported. No tools should be left in a location not meant for storage.
Operating heavy machinery
Machinery should be in full working condition, equipped with all the manufacturer’s safety guards installed.
Any time a malfunction or defect is noticed, alert the maintenance department, and review the equipment’s instruction manual. Hazardous material handling continues to be an underrated risk in many industries. If you are not trained properly in the technical aspects of operating certain machinery, don’t use it. After work is done, remember to shut down the machines.
Maintaining Cleanliness
Especially during the coronavirus pandemic, keeping a clean work area does wonders when it comes to preventing accidents. A clean, organized area helps create a better, less stressful work atmosphere. Many factors should be considered, including proper ventilation and lighting fixtures.
Keeping a clear head
Production facilities can pose a lot of risks, so maintaining a clear head is mandatory. Working under the influence of drugs or alcohol should be forbidden. People who must take certain medications that have side effects should notify their superiors.
Companies should ensure their workers are aware of all safety procedures, and that the work environment is safe. The rules must apply to everyone, and each breach in following them should be addressed and/or punished. No employee should ever have to worry about working in unsafe conditions, because when it comes to factory work, the consequences can be severe.
Costly slips and falls
Slips, trips, and falls can impact the bottom line hard, and severely hinder goals of making a safer environment for a company’s most valuable asset: its employees. Adding anti-slip floor mats, coatings, ladder rungs, plates and tapes has been a sound practice for years and helps save lives. Such products should far exceed the U.S. Occupational Safety and Hazards Administration (OSHA) and Americas with Disabilities Act (ADA) guidelines and be extremely durable.
Some of the coatings available can handle an 18-wheeler driving over them 24 hours a day and protect the truck driver from slipping when gassing up in wet or slippery areas. Whatever the nature of the traffic or contamination making the surface unsafe and slippery, the right solution is out there. Secure ladders so that others won’t trip on them or lose traction while
pulling material off a truck when the doors are open on a rainy day.
Source of Injury/Illness in the Paper Manufacturing Industry
Harmful substances & environments 5%
Transportation incidents 4%
Overexertion & bodily reaction 26%
Falls, slips, trips 19%
Contact with object, equipment 46%
Source of Injury/Illness in the Paper Manufacturing Industry
Floors, walkways, ground surfaces 11%
Chemicals, chemical products 2%
Furniture, fixtures 3%
Handtools 5%
Vehicles 9%
All other 9%
Containers 14%
Machinery 23%
A thorough check of the entire facility by the in-house maintenance crew can be performed with minimal or no downtime. It’s effective at finding hotspots that may have been forgotten about or overlooked. Any areas, including a loading-dock diamond plate (a forklift operator’s nightmare), concrete ramps, slick grating or uneven walkways can be noted as well. Walking the area with the plant or operations manager on a regular basis is wise because they usually know where safety problems may be or may start.
Occupational Hazards
To create a safe and effective work environment, employees must be able to identify the occupational hazards that lurk around every corner. Even fiber dust produced during the papermaking process can pile up on the ground and cover machinery. When airborne, this dust creates an explosion hazard and can also cause respiratory problems if inhaled by workers (see related article in this newsletter).
Chemicals used in paper making can also be hazardous. To avoid injury, it’s important that all substances are labeled properly, and the appropriate PPE is worn to avoid exposure problems. Showers and eyewash stations should be clearly marked and located in each employee work area.
Ventilation is key: Hot surfaces and high temperatures within paper mills due to the friction and steam produced during the papermaking process cause heat stress. Without the proper ventilation, employees may succumb to heat stroke if precautions aren’t taken to properly ventilate the work area. Employees must be aware when working near sharp tools and surfaces, edges, and machinery. Blades and moving rollstock on machines can cause scratches, cuts, and even amputations. With most cutting occurring on the hands, it’s critical for employees to have proper hand protection. Ear protection is also a must to protect hearing if noise reaches high levels. It’s imperative that pulp and paper companies adopt preventative measures such
as purchasing low-noise machinery, noise barriers and adequate ear protection.
While these measures may require cost expenditure, it’s better to be proactive versus reactive. For more safety tips, see the National Safety Council’s website nsc.org.
Leave a Reply

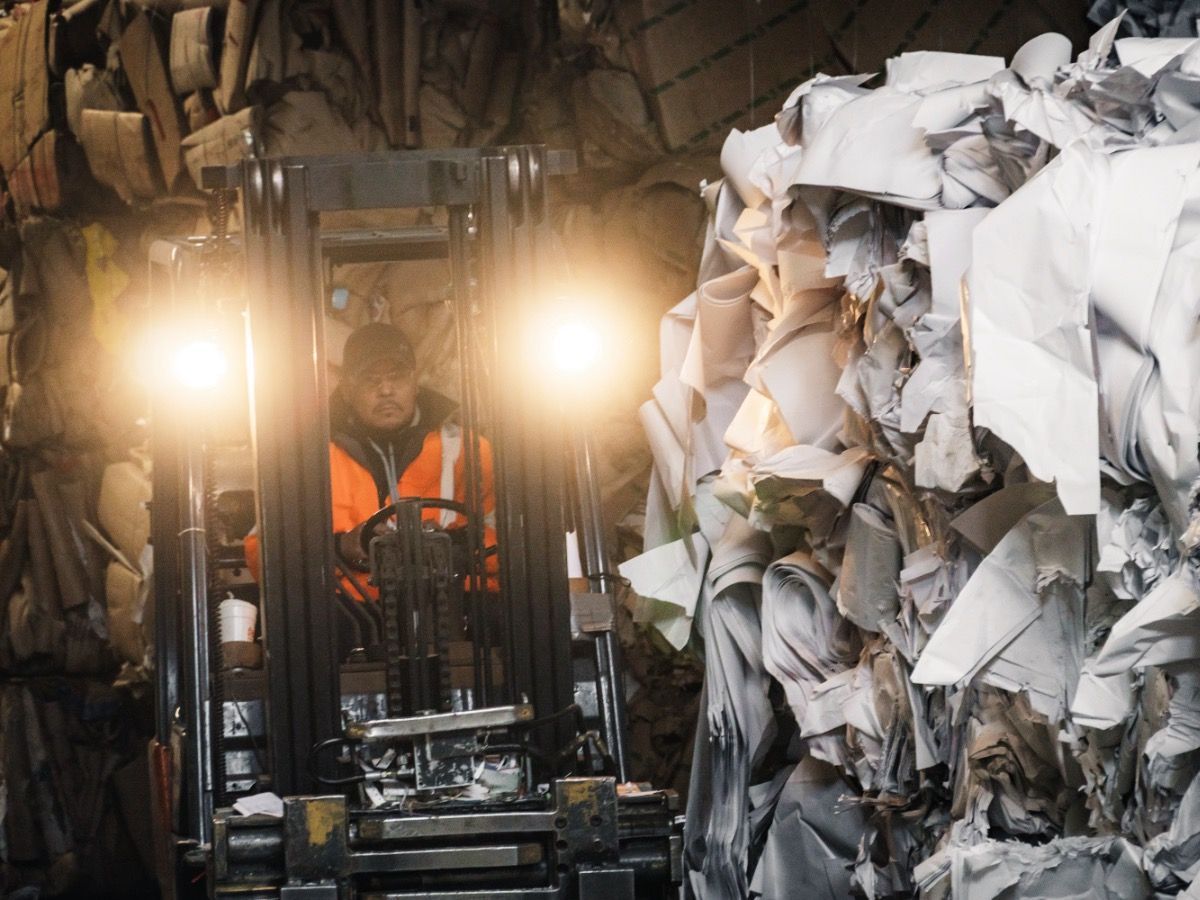
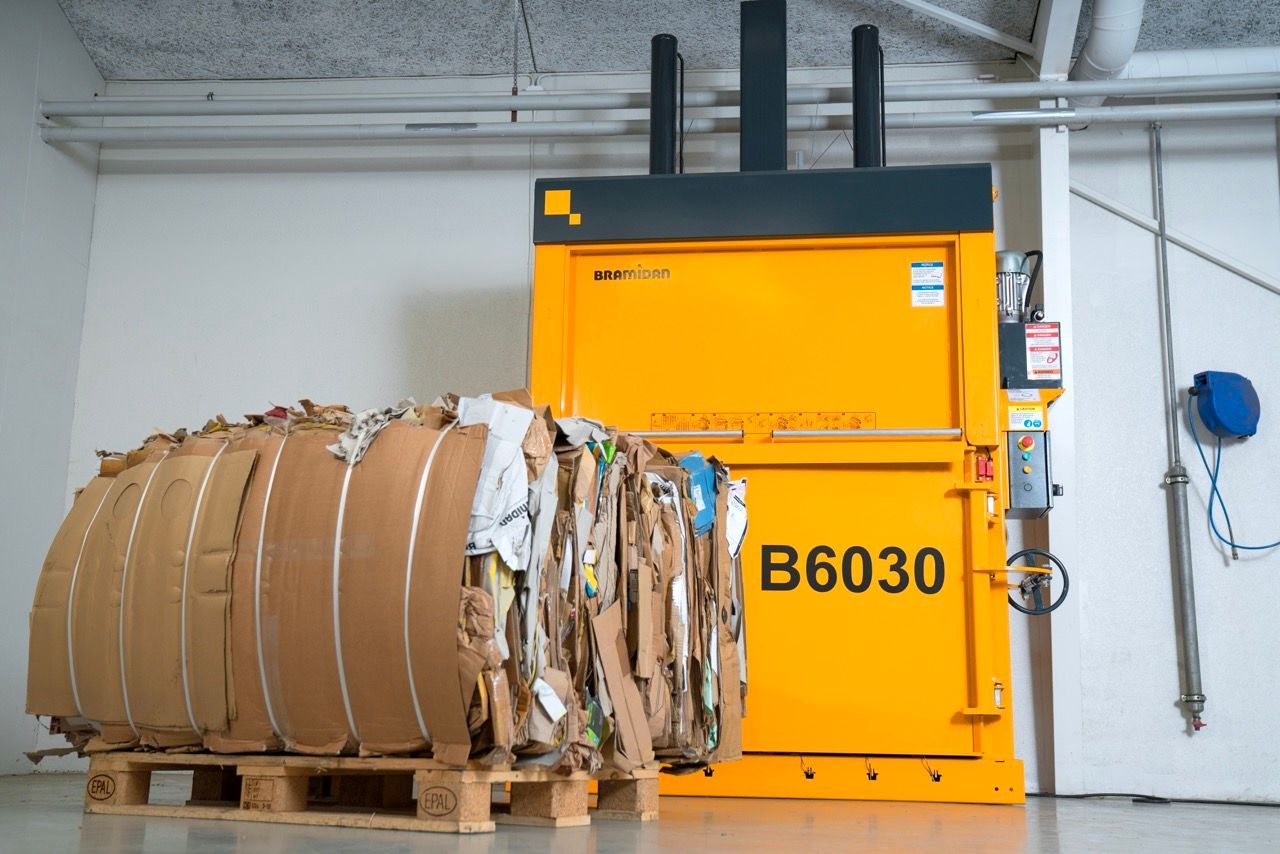