MAPR Blog--Light Load Charges
April 13, 2022
Don’t Come Up Short: Avoiding Light Load Charges
Recycling logistics teams must meet new challenges motivated by transportation costs savings and ecological efforts. Optimizing trailer load pack patterns can help.
If there was ever a case where weight loss was a problem, this is it: Right now, like everything else, logistics and shipping costs are quickly rising for paper waste suppliers that ship bales of their recyclable paper waste mill-direct. Trouble is, trailer loads of the recyclable paper waste that don’t hit the requisite 20-ton (40,000-lb) weight requirement set by most pulp and paper mills get slapped with what are called Light Load freight charge backs.
These charges can add up, and hinder recycling operations from delivering real value to customers. Monitoring them regularly, as well as the weights of trailer load waste is a must. That’s why Mid America Paper Recycling advises its supplier partners to be as accurate and efficient as possible when baling their paper waste. It can make a powerful impact on the bottom line, explains Mid America’s President Paul Pirkle.
“It’s worth reviewing any light load charges passed on by the paper mills,” Pirkle says. “Light load charges are usually assessed when a supplier’s load of paper waste -- regardless of the type of paper -- doesn’t weigh the required 40,000 pounds (or 20 tons) most mills require. The charges can be a significant drain on profitability, and can have been avoided with better visibility into the loading process.”
For example, if your mill-direct freight cost to ship a load of recyclable paperboard weighing the standard 20 tons is $1,000, and the load weighs 19 tons (or one ton less than the acceptable standard), a charge assessed to the Light Load would be $50 ($1,000 divided by 20 = $50). That charge will be assessed on a per-ton basis for every load weighing less than 20 tons. If your trailer load is two tons short, a Light Load charge would be $100.
“We always caution companies about weight requirements for shipping trailer loads,” Pirkle explains. “Paper waste suppliers should focus on hitting the 20-ton or 40,000-pound weight target, no matter what type of paper waste they’re shipping. Otherwise, they will be charged back for any loads weighing less, divided by their cost of shipping the load into the site. With freight costs increasing in general, these charges are intensified.”
Increasing baling efficiency
There are several reasons a load can be underweight. Mid America advises suppliers to examine their truck loading patterns with a couple of “smart” solutions that will boost the efficiency of loading operations and maximize bale weights. By working smart, you can increase cube efficiency in the trailer, higher accuracy, worker safety, and customer satisfaction with Mid America Paper Recycling’s assistance.
There are a few important considerations suppliers can use with underweight trailer loads, Pirkle says. “Check to make sure that you are regularly maintaining your baling equipment with the recommended preventive maintenance and also confirm that your baler is achieving the best bale compression possible per the manufacturer's specifications.”
Bales weigh between 900 and 1,500 lb. Most baling systems available on the market are easily able to compress (or densify) a bale of paper waste material into a tight, compact unit weighing 1,250 lbs. or more.
“If your bales weigh less than 1,000 pounds, they can be too light and could cause an entire trailer load to be short of the target weight (40,000 lbs.),” Pirkle says. “The baler is one of the first things we look at when we hear that trailer loads are under weight. Examining the baling procedures and inspecting the baling equipment to ensure that it’s properly maintained are important. Make sure the equipment is working properly and operating with the correct compression.”
Second, if the baler(s) is working properly, and the loads still aren’t hitting the target weight, check the loading pattern. In the haste to get a trailer on the road, bales of paper waste might be loaded incorrectly.
“Loading patterns are the next thing we look at,” Pirkle mentions. “Share what your bale patterns looks like. We will then confirm that the correct pattern is being used and that the bales are being properly, and safely, loaded into the trailer so the bales will be received by the mill properly.”
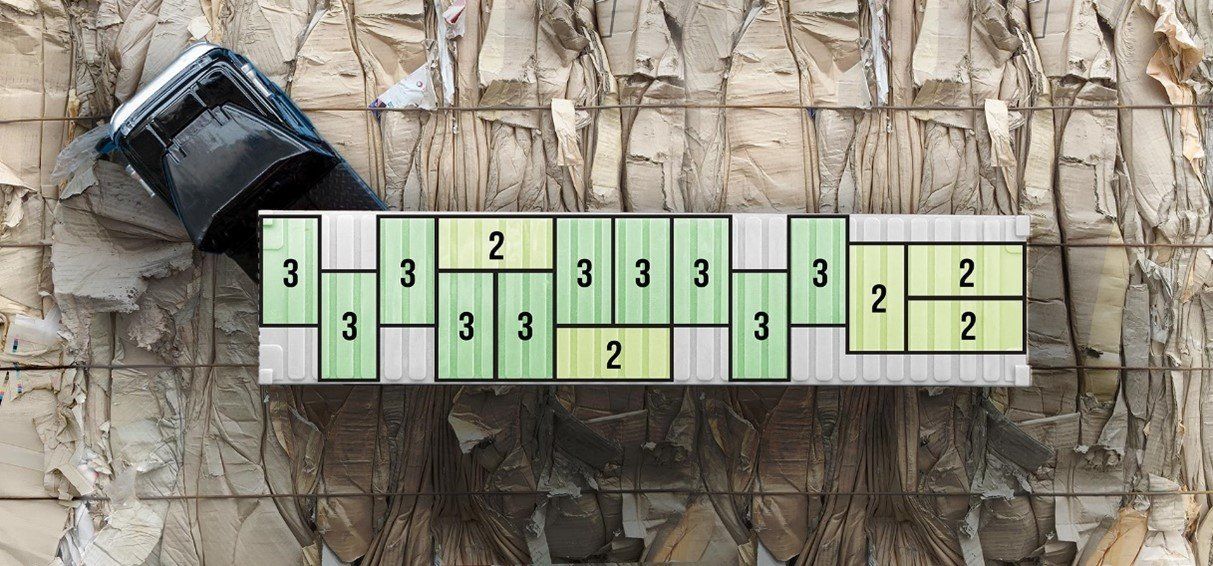
The chart above shows a trailer loading pattern Mid America custom developed for a supplier. It is imperative to load the last two bales in the truck perpendicular to the other bales for safe unloading.
Optimizing pack patterns
A standard 53-ft.-long truck trailer should hold 36-39 bales, Pirkle adds. If that checks the box, and the bales weigh what they should and are being loaded into the truck according to the correct pattern, what if they still come up underweight?
“Then, we look at the rest of the operation,” Pirkle replies. “In instances where we visit the supplier’s site to determine the cause of the light loads, we check their baler’s performance and re-examine the loading pattern. We may also find something else within the operation that might need correcting. In most cases, we’ll be able to improve the loading pattern design for more efficiency. We also have the supplier post diagrams of scaled drawings of the pack pattern and loading instructions for easy reference whenever they need it. We then load a trailer using the new format, to see how many bales will fit.”
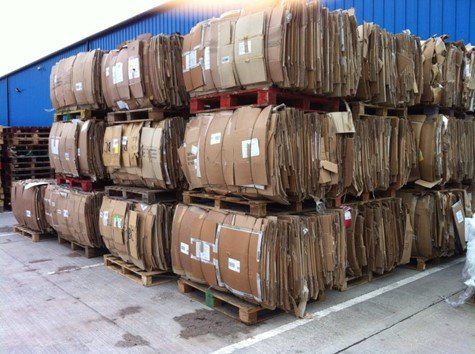
Mid America may suggest that suppliers invest in a scale to ensure they’re getting accurate weights, Pirkle points out. “Light Load charges can be completely avoided. Checking the loading pattern and ensuring your baler is well maintained will ensure that you are continually turning waste streams into profit streams.”

For printing and packaging firms, floor space is a critical resource directly tied to productivity, safety, and profitability. Operating under typically tight profit margins, these companies cannot afford inefficiencies that hinder operations or add unnecessary costs. Yet, in many facilities, valuable floor space is wasted on scrap and trim waste from the paperboard manufacturing and converting process. Gaylords of loose material waiting to be processed and bales awaiting pickup can create bottlenecks, disrupt workflows, and eat into already slim margins. At Mid America Paper Recycling, we provide timely solutions to help manufacturers reclaim their floor space and protect their bottom line. Here’s how: The Hidden Costs of Wasted Floor Space Inefficient use of floor space doesn’t just limit operational effectiveness—it carries significant financial and operational consequences. Here’s what’s at stake: High Real Estate Costs : Manufacturing and warehouse space is expensive. According to Prologis, the annual cost for warehouse space averages $13.20 per square foot , including base rent and operating expenses. A facility dedicating 1,000 square feet to waste storage could incur $13,200 annually in avoidable costs. Safety Risks and Workplace Injuries : Cluttered floors with bins of loose material and stacked bales create hazards that increase the risk of workplace injuries. The National Safety Council reports that the average cost of a medically consulted workplace injury exceeds $40,000 , factoring in productivity losses, medical bills, and administrative expenses. Missed Revenue Opportunities : Every square foot dedicated to waste is a square foot unavailable for revenue-generating activities. For example, a production machine occupying 1,000 square feet could generate $100,000 to $500,000 annually in additional revenue. Increased Labor Costs : Managing waste on the plant floor is time-consuming. Employees spend hours moving, organizing, and handling waste instead of focusing on higher-value tasks. At an average wage of $20 per hour , one additional hour spent daily on waste management can cost a company $5,000 annually per employee . How Mid America Paper Recycling Reclaims Space Reclaiming floor space starts with understanding a facility’s unique challenges. Through our waste audit services , we identify inefficiencies in waste management handling practices in your plant facilities and provide customized solutions to optimize space utilization. Trailer Spotting: A Game-Changer for Floor Space One of the most effective strategies we offer printers and board converters is trailer spotting. Instead of storing waste on the plant floor, a dedicated trailer is stationed on-site to accumulate scrap and trim waste, and then rotated back to our recycling facility for materials processing. Maximizes Plant Space : By removing bales and scrap from the floor at key intervals, plants can free up hundreds or even thousands of square feet for production or finished goods storage. Improves Safety : Clear, clutter-free floors reduce the risk of accidents and ensure smoother workflows. Cuts Handling Costs : Employees spend less time managing waste, which translates to significant labor savings. Streamlines Operations : Trailers simplify the waste management process, ensuring efficient material handling and faster pickups. Faster Financial Return on Recyclables : By consolidating and efficiently managing scrap materials in a trailer, recyclables can be transported directly to mills more frequently. This reduces delays, accelerates payments, and ensures more consistent cash flow tied to a recycling program. For example, one large printing client reduced their reliance on floor space for bales by 50% , enabling them to install additional equipment and increase production capacity. Execution in Action At Mid America Paper Recycling, we deliver results through precise execution of recycling programs. Our Chicago-based facility processes 51 different paper grades using advanced baling systems and a fleet of 125 trailers in our logistics network. By leveraging our infrastructure and consulting expertise, we help customers reclaim floor space, reduce costs, and maximize profitability year after year. Partner with Mid America to Reclaim Your Space For any packaging manufacturer, the value of floor space cannot be overstated. Don’t let waste take up space that could be driving your business forward. Let Mid America Paper Recycling help you optimize your operations, starting with a free waste audit to discover how we can help you unlock the hidden value in your facility.
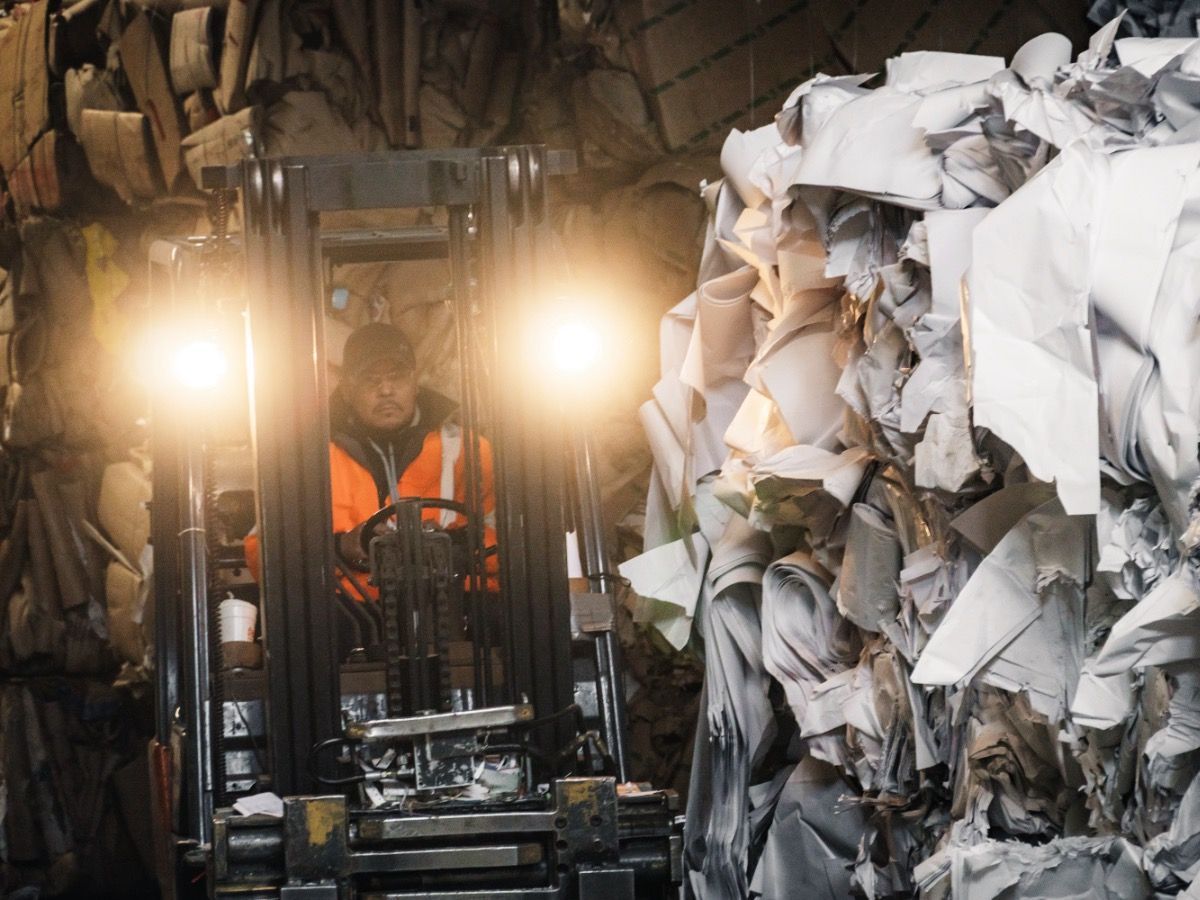
As Vince Lombardi once said, "Talent and a good game plan each on their own are not enough to win. Execution is everything." This timeless insight rings especially true in the recycling industry, where results hinge on not only having the right resources but also leveraging them with precision and consistency. At Mid America Paper Recycling, execution is our hallmark, honed over decades of practice and refinement. From Talent to Teamwork At the heart of Mid America Paper Recycling’s success is our experienced and dedicated team. With generations of expertise, we’ve cultivated a culture where execution is second nature. Our employees undergo training, and our game plan for customer support is practiced and optimized continually, ensuring consistent excellence in every service we provide. From plant operations and brokerage, to transportation and customer service, every team member understands that their role is pivotal in delivering the quality and reliability our clients expect. The Game Plan: Precision and Purpose Winning in recycling, much like in sports, requires a well-orchestrated strategy. Here’s how we execute our game plan to help our supplier-partners turn waste into value: Waste Stream Audits Each client engagement begins with a detailed audit of their waste streams, mapping the journey of recyclable materials from generation to exit. For example, at one facility, our audit identified inefficiencies in sorting, allowing us to recommend adjustments that increased recycling rates by 20% and reduced disposal costs significantly. 2. Maximizing Revenue with Mill Direct Shipments By leveraging our strong relationships with mills worldwide, we ensure that materials are shipped directly to the most advantageous destinations. For instance, a paperboard converter client generated $140,000 in new revenues after we helped them implement a dedicated dock for mill-direct shipments. 3. Enhancing Operational Efficiency Our innovative handling solutions reduce labor costs and improve safety. In one case, we introduced custom receptacles for a printing facility, eliminating the need for double handling of scrap materials and reducing workplace injuries by 15%. 4. Uncovering Hidden Value Misclassified materials and overlooked recycling opportunities are common pitfalls in waste management. For example, we worked with a fulfillment center customer to reclassify their "mixed paper" waste stream into higher-value grades, increasing their recycling revenue by 30%. 5. Providing Accountability and Transparency Timely reporting and payments are standard operating procedure at Mid America. One client noted improved decision-making after implementing our detailed quarterly reports, which highlighted cost savings and environmental contributions across all their facilities. Execution at the Processing Plant Our Chicago-based facility exemplifies what great execution looks like in recycling services. Equipped with state-of-the-art baling systems and supported by a fleet of over 125 trailers, our plant processes 51 different paper grades of recyclables. By meticulously sorting, baling, and shipping materials, we ensure that our clients' waste streams are transformed into high-quality commodities for mills across the globe. Why Execution Sets Us Apart Our Chicago-based plant operations set us apart by ensuring unmatched reliability. Unlike brokers who rely solely on external processors, we maintain control over quality and consistency, virtually eliminating the risk of mill rejections or downgrades—a common issue with third-party processors. Our decades of experience also provide the flexibility to adapt swiftly to changing market conditions and evolving client needs. Most importantly, our commitment to execution consistently delivers tangible results, from cost savings to increased revenues, directly impacting our clients’ bottom lines. A Commitment to Winning—For You In recycling, as in football, the difference between a good performance and a championship win lies in flawless execution. Mid America Paper Recycling doesn’t just play the game; we play to win—for our clients, our planet, and our future. As we approach the Super Bowl, let’s remember: talent and a game plan are essential, but execution is what turns potential into victory. If you're ready to take your recycling program to the next level, let us help you execute a winning strategy. Take our free Waste Audit Survey to get started today.
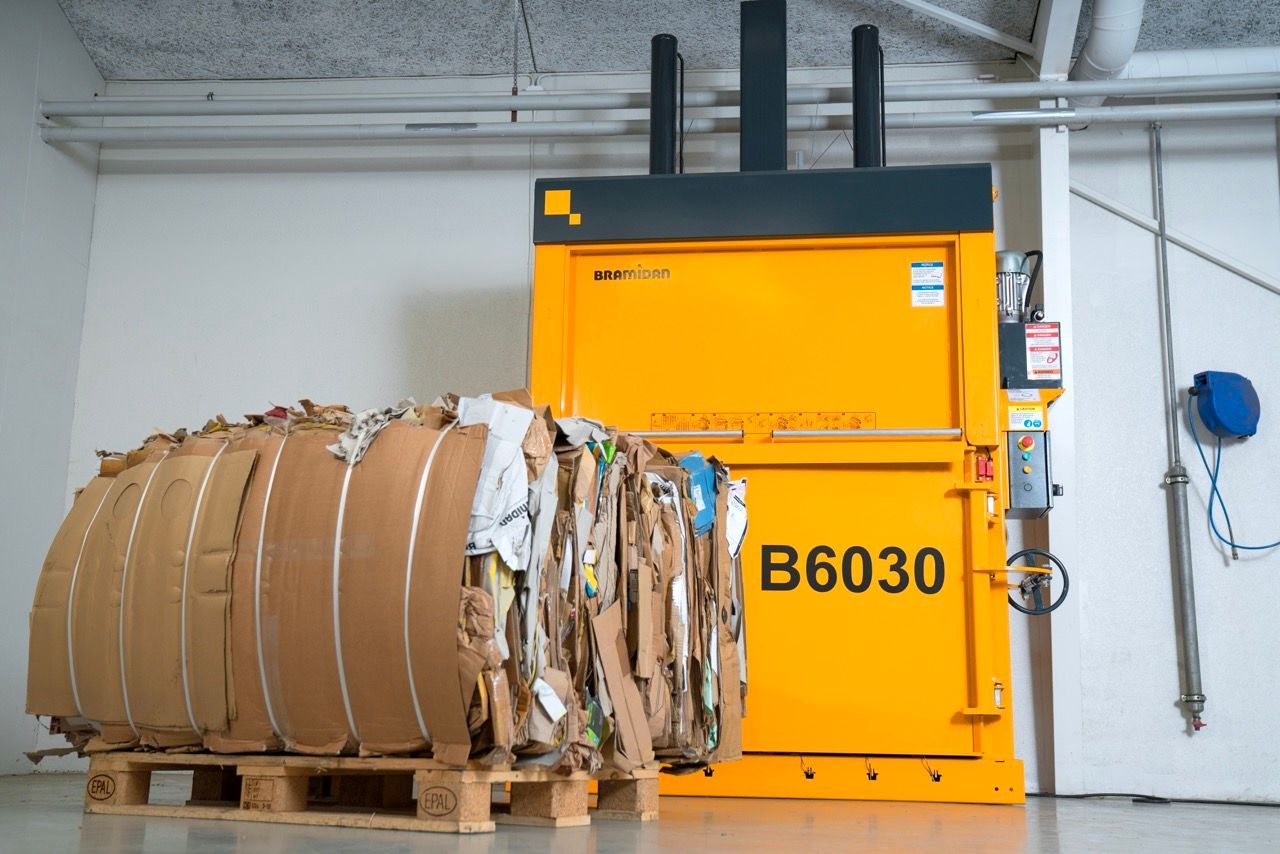
The paper and cardboard recycling market has evolved dramatically over the past decade. Once viewed as a straightforward waste collection activity, scrap and paper recycling has become a sophisticated process driven by innovation, partnerships, and the growing demand for sustainable practices. For printing and packaging converters as well as box plant managers, this evolution offers opportunities to increase revenue in your operations while meeting sustainability goals. As a fourth-generation independent broker, processor, and exporter of recovered paper, Mid America Paper Recycling has witnessed these changes firsthand over decades. We’ve adapted and innovated to help our partners thrive in this dynamic market. As we enter 2025, let’s dive into the key trends shaping the future of recycling and how your business can stay ahead. The Evolving Recycling Landscape The days of simply tossing recyclable materials into a gaylord bin and forgetting about them are long gone. The recycling market now prioritizes extracting maximum value from every paper grade in every waste stream in your facility. This shift is driven by: Stringent environmental regulations pushing companies to reduce landfill contributions Consumer demand for sustainable products, prompting brands to adopt eco-friendly packaging Advances in technology, enabling more efficient sorting and processing of recyclable materials These changes have transformed how companies like Mid America Paper Recycling work with our supplier-partners, moving from a reactive service model to more of a proactive, strategic partnership approach.