Quality baling machines can provide years of reliable service life if they’re maintained and serviced regularly. You wouldn’t drive a car for years without a service; why risk the health of your baler equipment?
An automatic baler can handle a large load of recyclable waste without much manual labor to prepare and tear down loads. Balers improve baling rates, which allows you to achieve recycling targets and make more money. Automatic balers also bundle waste tightly, which keeps them compact and more organized while keeping the warehouse neat. Compacting bales using either a horizontal or vertical baler and securing them with bale ties streamlines the recycling process, saving time and money in the long run by reducing the volume of recyclable materials, transportation costs, and the use of warehouse space.
“Baling systems provide more productivity and profitability,” says Michael Schwinn, Vice President – Sales & Marketing – at American Baler Co., Bellevue, OH. “Handling recycling materials is typically handling the scrap end of the product or the packaging process. Balers are the most effective method of handling waste material. Automatic [horizontal] balers can be 10 times more efficient than compactors or vertical balers.”
Finding a baler for the size and scope of your recycling operation isn’t always easy, but Mid America Paper Recycling can help businesses review their current recycling processes and suggest baling equipment, such as systems from American Baler, which can maximize their total expense and revenue.
Jerry Fick of Great Lakes Recycling Services, a Grant Park, IL-based waste management services firm that also services and sells new and used recycling equipment, recommends regularly and properly maintaining the equipment to prolong its useful life. “If buying a new baler, be sure to look for one that can process your expected volumes. Running large volumes of recyclable waste creates the need for high-performing horizontal baling equipment.”
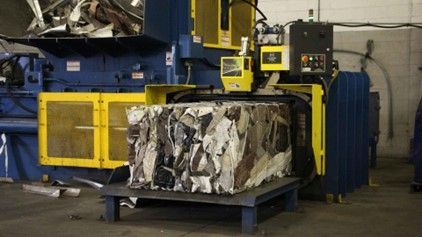
Photos courtesy of American Baler
“Higher waste volumes often justify the investment in a baler because there’s better cost per use,” Schwinn explains. “The more production needs you have, the more important it is that all system components be synchronized. Higher valued labor typically means you can justify a system with automatic tying. Materials that are difficult to bale, such as large cardboard pieces, require a larger infeed, an infeed conveyor, or a pre-shredder. But regardless of the volumes and waste sizes, buyers want to ensure the material is easy to load into the baler and the bales can be easily tied (manually or automatically).”
Schwinn adds that producing heavier bales saves on baling wire costs. “Wire costs can be one-third higher if you’re making a 1,200-pound bale versus a 1,600-pound bale and you bale 200 tons a month. The same applies to smaller vertical balers but those must factor in both baling wire and the added labor costs of manually tying off the baler more.”
Care and cleaning
Both experts advise learning about the machine’s safety features and about the machine’s computerization (if applicable) and human-machine interfaces. Keeping the baler well maintained is vital, Fick adds. “Remember to follow the manufacturer’s manual that came with the machine and hire an experienced repair technician or mechanic when repairs are necessary. It’s a good idea to perform a daily cleaning routine of the system and stay on a recommended schedule.”
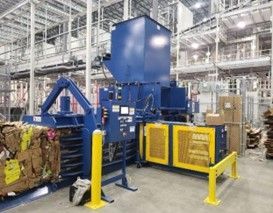
Schwinn agrees. “We suggest that customers perform daily and monthly checkups. Making repairs or adjustments should be the first level of service. Find out how easy it is to keep systems with automatic bale tying cleaned and aligned and find out how easy it is to purchase parts.”
Keeping the equipment optimized means keeping it clean, he notes. “Keeping a clean work area is safer and more productive. A clean baler helps you observe the start of a potential problem. A drip of oil at the power unit might easily indicate the need to check fittings and tighten a hose fitting, for example. If a power unit has material and dust covering it for weeks, you might never see the drip until it becomes a major problem.”
Schwinn says that today, customers look at scrap-handling equipment differently than they did pre-COVID. Despite issues with the supply chain, the changing market conditions for recyclable materials, less in-house labor, and other recycling concerns, “customers want equipment that assures scrap is handled just once and most efficiently. Fewer bales mean greater production per employee. Companies are replacing older baling equipment because if they don’t, they fear they might lose a valuable maintenance technician. Automatically baling your waste materials will provide you with top value for the material, regardless of commodity price swings.”
If purchasing new baling equipment, plan ahead, the experts advise. With high demand for hydraulic and electrical components, lead times on baling equipment purchases are usually about 40 weeks, depending on the manufacturer.
No doubt, baling equipment helps many recyclers increase their revenue, Fick states. “A baler is a wise investment. Balers make the materials ready for the market.”
Mid America Paper Recycling can help you determine your baling equipment needs. To request our free, quick, Waste Audit Survey, go to https://bit.ly/2OI2o0Z.


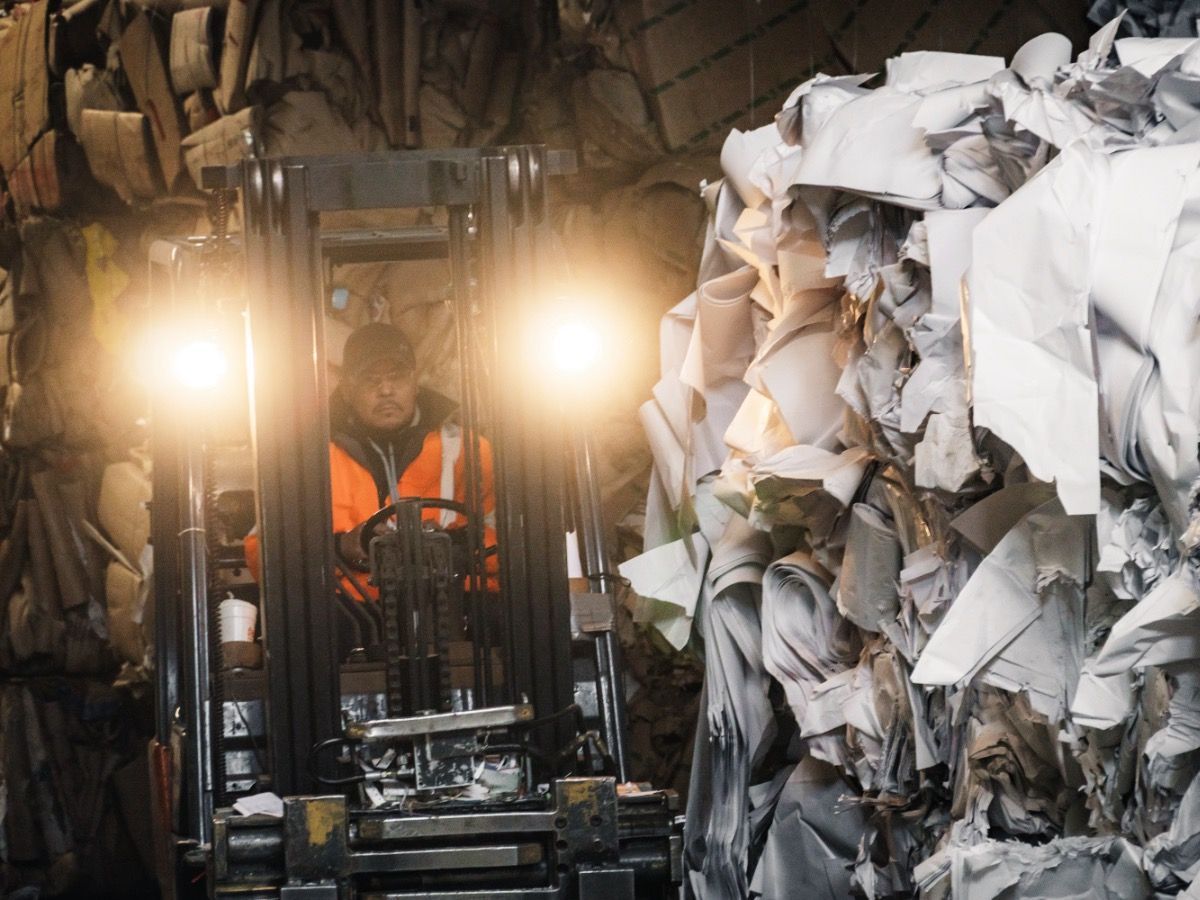
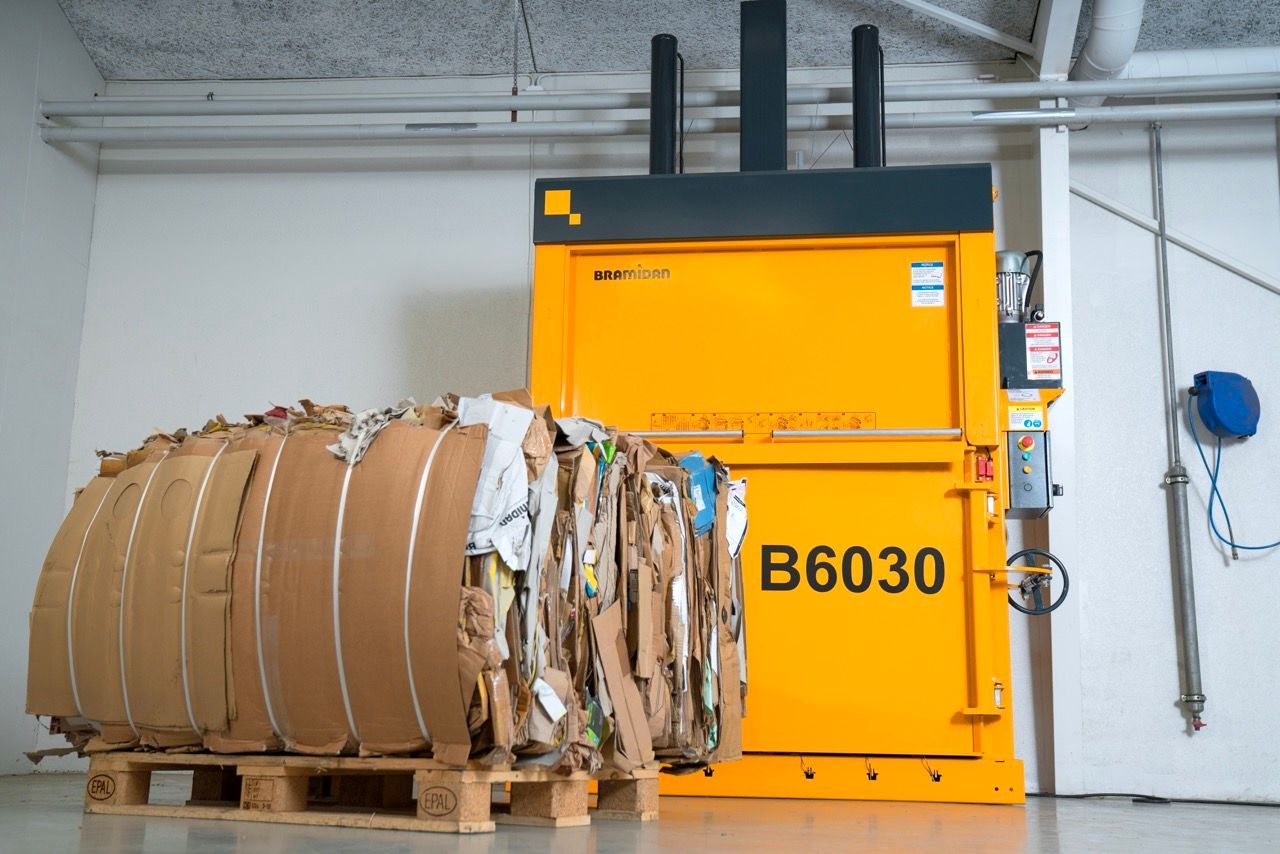